CAN-Kommunikation als Hardware-In-The-Loop-Simulation
Per Raspberry Pi zum digitalen Zwilling
Digitale Zwillinge sollen den Zustand und das Verhalten ihres realen Pendants wenn möglich in Echtzeit wiedergeben und dadurch schnellere und präzisere Reaktionen auf die reale Situation im Feld ermöglichen. Im Rahmen einer Master-Arbeit an der RWTH Aachen wurde ein virtuelles konfigurierbares Testsystem entwickelt, das die CAN-Kommunikation einer Maschine mit einer realen SPS als Hardware-In-The-Loop-Simulation abbildet. Dafür werden Slave Stacks über Node Red angesteuert und über das CANopen-Framework CANFestival auf einem angebundenen Kleinstrechner ausgeführt, z.B. einem Raspberry Pi.
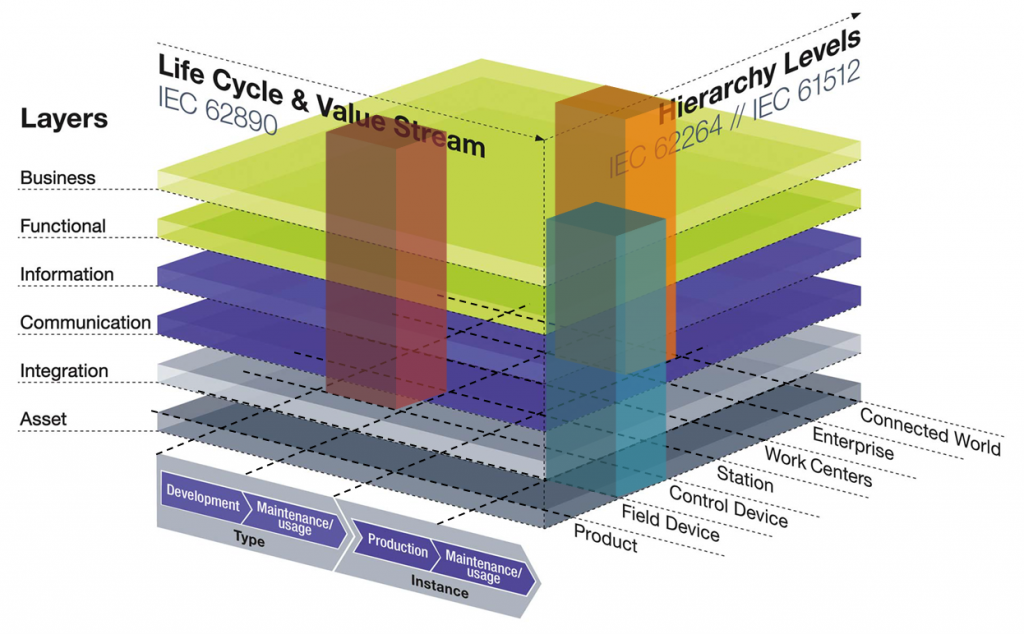
Digitale Zwillinge sind für Kleinserien und Sondermaschinen sehr relevant, da es selten wirtschaftlich akzeptabel ist, für jedes Produkt in jeder Variante ein Testsystem vorrätig zu haben. Somit können Serviceeinsätze nur unter erschwerten Bedingungen unterstützt werden; ein sicherer Erfahrungsgewinn zur Weiterentwicklung ist zwischen zahlreichen Kommunikationsschnittstellen nicht gegeben. Dies kann mithilfe eines digitalen Zwillings verbessert werden. Die Entwickler können direkt am Prozess teilnehmen und somit mehr Erfahrung aus der vorhandenen Situation ziehen. Gleichzeitig kann die Problemursache leichter behoben werden: Einerseits durch die verbesserte Datenlage und andererseits weil weniger Kommunikation zwischen Außendienst und Entwickler notwendig ist - dadurch bleibt mehr Zeit zum Beheben des Fehlers und es können weniger Missverständnisse entstehen. Zudem besteht die Möglichkeit Fehler zu antizipieren, falls das problematische Maschinenverhalten bereits bei einem anderen System beobachtet werden konnte. Im Idealfall können Probleme gelöst werden, bevor sie entstehen.
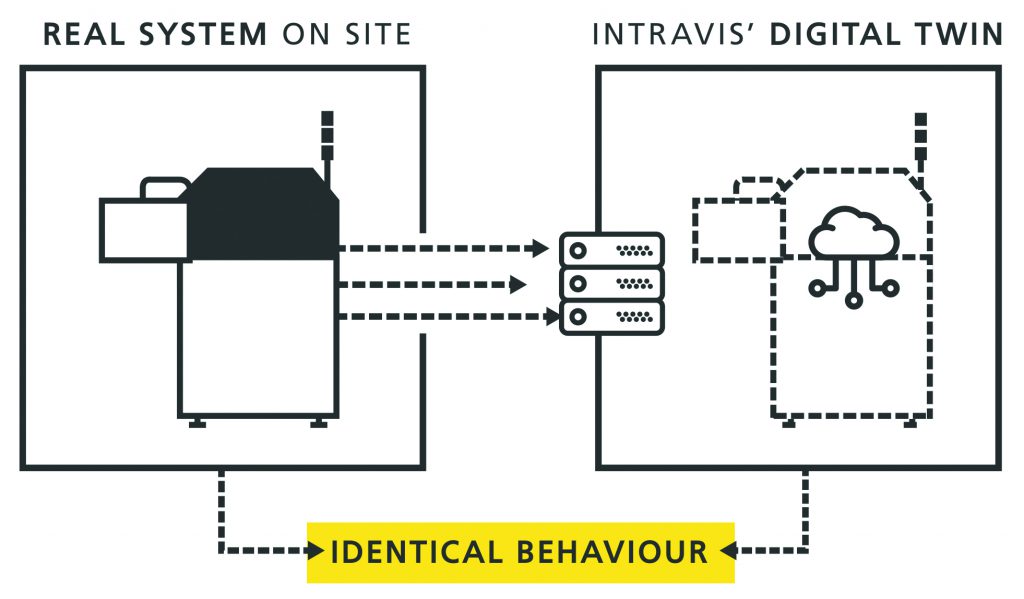
Simulation als Grundlage
Als Grundlage für den digitalen Zwilling ist eine Simulation notwendig. Als Ansatz zur Simulation des vorliegenden CANopen-Bussystems bietet sich ein Hardware-In-The-Loop-Aufbau an. Die Hardware-Seite in Form der verwendeten Maschinen-SPS wird über ein reales Bus Kabel an einen Simulationsrechner angeschlossen. Um die unterschiedlichen Busteilnehmer darzustellen, werden Slave Stacks mithilfe des CANopen-Frameworks CanFestival implementiert. Sie erhalten über die elektronischen Datenblätter der verwendeten Geräte ihre Identität. Darin enthalten sind alle Variablen, die das entsprechende Gerät definieren. Die Slaves greifen parallel auf den Bus zu und können somit in Echtzeit mit der SPS kommunizieren, die resultierenden Antwortzeiten sind teilweise geringer als die der realen Maschine. Zusätzlich wird die SPS mit der Benutzeroberfläche der simulierten Maschine verbunden, sodass auch deren Kommunikation Teil des simulierten Systems ist. Die Summe der lokalen Infrastruktur - im Folgenden als Simulationssystem bezeichnet - kann z.B. auch für virtuelle Inbetriebnahmen eingesetzt werden.
Von der Simulation zum digitalen Zwilling
Auf dem Simulationssystem aufbauend wird eine Möglichkeit zur Akquise von Betriebsdaten benötigt. Zu diesem Zweck wird ein Kleinstrechner, z.B. ein Raspberry Pi, mit dem Bussystem der Maschine verbunden. Die Kommunikation der realen Maschine wird aufgezeichnet und an einen Cloud-Service übermittelt. Dabei können konkrete Ereignisse ausgewählt werden, bei deren Eintreten der vorangegangene Zeitraum nochmals mit einem entsprechenden Vermerk gesendet wird. Auf diese Weise lassen sich einzelne Fehlerszenarien schneller finden und analysieren. In der Cloud kann man die Daten mit flexibel angemieteter, bei Bedarf enormer Rechenleistung analysieren. Zusätzlich ist die Einbindung von unternehmensexternen Kompetenzen möglich.
Integration und Datenakquise
Für die Integration des Kleinstrechners gibt es mehrere Möglichkeiten. So können die Mitarbeiter im Außendienst bereits im Feld befindliche Systeme anbinden. Auch ein fester Einbau des Kleinstrechners in das Kundensystem ist denkbar. Für eine möglichst breite Abdeckung sollten vor allem neu verkaufte Systeme entsprechend ausgerüstet werden, entweder als Sonderausstattung oder als Bestandteil des Standards.. Darüber lassen sich große Mengen an Betriebsdaten generieren und analysieren, gleichzeitig wird für den Anwender die Anlagenverfügbarkeit erhöht.
Erwecken des digitalen Zwillings
Mit den nun vorhandenen Daten und dem Simulationssystem kann der digitale Zwilling erweckt werden. Dafür muss lediglich das richtige Programm auf die SPS aufgespielt werden und der virtuelle Bus dementsprechend konfiguriert werden. Daraufhin geben die Slave Stacks die Kommunikation der realen Maschine anhand der Aufzeichnung wieder. Das führt im Umkehrschluss dazu, dass sich die SPS samt verbundener Benutzeroberfläche gemäß ihrem realen Vorbild im Feld verhält. Dabei besteht die Wahl den Zwilling als Live-Version zu erstellen, gespeist aus einer laufenden Übertragung, oder als Rückblick, mit aus dem Archiv der aufgezeichneten Kommunikationshistorie stammenden Daten. Mithilfe des digitalen Zwillings können die Maschinenzustände und das Verhalten von SPS und Benutzeroberfläche analysiert werden. Zusätzlich kann das Simulationssystem im Anschluss auf dem Zwilling aufbauen, entweder durch manuelle Eingaben oder das Abspielen von selbst erstellten bzw. aufgezeichneten Szenarien. Damit kann das Verhalten des dargestellten Systems unter verschiedenen Einflüssen getestet und wenn nötig angepasst werden.
Anwendung in der Praxis
Die Firma Intravis ist Hersteller von Systemen zur optischen Prüfung von Kunststoffteilen. Typische Prüfobjekte sind Verschlusskappen und Vorformlinge für Flaschen sowie Aufdrucke und Etiketten von Verpackungen. Die beschriebene Entwicklung des digitalen Zwillings fand als Masterarbeit, in Kooperation mit dem Werkzeugmaschinenlabor (WZL) der RWTH Aachen statt, um eine Verbesserung der Serviceabläufe und Entwicklungsbedingungen zu erzielen. Die betrachteten Maschinen setzen sich aus drei Hauptkomponenten zusammen: einem Industrie-PC mit der Benutzeroberfläche, der SPS und dem angebundenen Bussystem und dessen Komponenten.
Digitale Zwillinge sollen den Zustand und das Verhalten ihres realen Pendants wenn möglich in Echtzeit wiedergeben und dadurch schnellere und präzisere Reaktionen auf die reale Situation im Feld ermöglichen. Im Rahmen einer Master-Arbeit an der RWTH Aachen wurde ein virtuelles konfigurierbares Testsystem entwickelt, das die CAN-Kommunikation einer Maschine mit einer realen SPS als Hardware-In-The-Loop-Simulation abbildet. Dafür werden Slave Stacks über Node Red angesteuert und über das CANopen-Framework CANFestival auf einem angebundenen Kleinstrechner ausgeführt, z.B. einem Raspberry Pi.
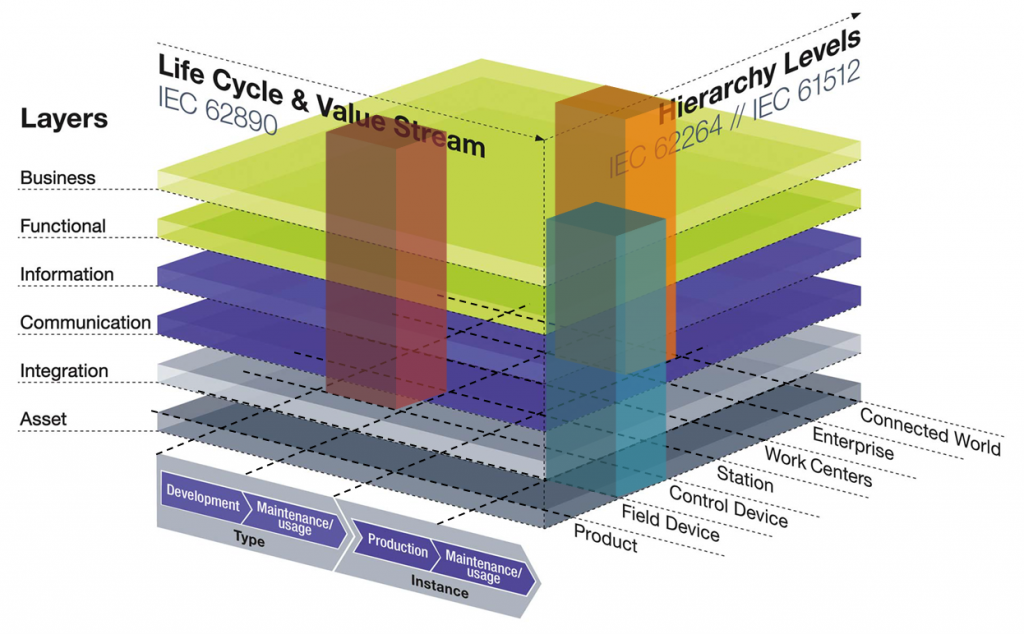
Digitale Zwillinge sind für Kleinserien und Sondermaschinen sehr relevant, da es selten wirtschaftlich akzeptabel ist, für jedes Produkt in jeder Variante ein Testsystem vorrätig zu haben. Somit können Serviceeinsätze nur unter erschwerten Bedingungen unterstützt werden; ein sicherer Erfahrungsgewinn zur Weiterentwicklung ist zwischen zahlreichen Kommunikationsschnittstellen nicht gegeben. Dies kann mithilfe eines digitalen Zwillings verbessert werden. Die Entwickler können direkt am Prozess teilnehmen und somit mehr Erfahrung aus der vorhandenen Situation ziehen. Gleichzeitig kann die Problemursache leichter behoben werden: Einerseits durch die verbesserte Datenlage und andererseits weil weniger Kommunikation zwischen Außendienst und Entwickler notwendig ist - dadurch bleibt mehr Zeit zum Beheben des Fehlers und es können weniger Missverständnisse entstehen. Zudem besteht die Möglichkeit Fehler zu antizipieren, falls das problematische Maschinenverhalten bereits bei einem anderen System beobachtet werden konnte. Im Idealfall können Probleme gelöst werden, bevor sie entstehen.
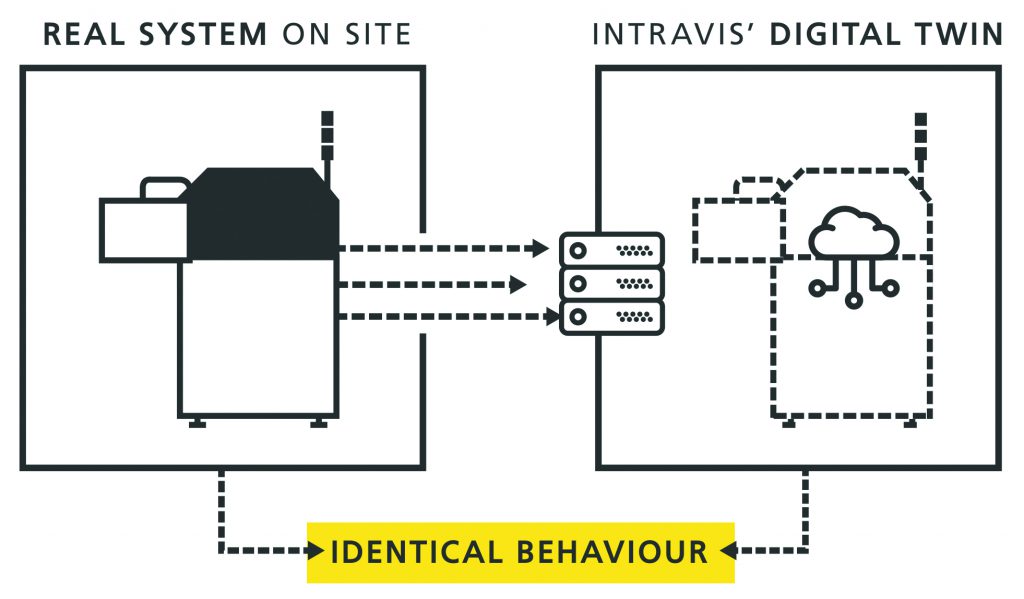
Simulation als Grundlage
Als Grundlage für den digitalen Zwilling ist eine Simulation notwendig. Als Ansatz zur Simulation des vorliegenden CANopen-Bussystems bietet sich ein Hardware-In-The-Loop-Aufbau an. Die Hardware-Seite in Form der verwendeten Maschinen-SPS wird über ein reales Bus Kabel an einen Simulationsrechner angeschlossen. Um die unterschiedlichen Busteilnehmer darzustellen, werden Slave Stacks mithilfe des CANopen-Frameworks CanFestival implementiert. Sie erhalten über die elektronischen Datenblätter der verwendeten Geräte ihre Identität. Darin enthalten sind alle Variablen, die das entsprechende Gerät definieren. Die Slaves greifen parallel auf den Bus zu und können somit in Echtzeit mit der SPS kommunizieren, die resultierenden Antwortzeiten sind teilweise geringer als die der realen Maschine. Zusätzlich wird die SPS mit der Benutzeroberfläche der simulierten Maschine verbunden, sodass auch deren Kommunikation Teil des simulierten Systems ist. Die Summe der lokalen Infrastruktur - im Folgenden als Simulationssystem bezeichnet - kann z.B. auch für virtuelle Inbetriebnahmen eingesetzt werden.
Von der Simulation zum digitalen Zwilling
Auf dem Simulationssystem aufbauend wird eine Möglichkeit zur Akquise von Betriebsdaten benötigt. Zu diesem Zweck wird ein Kleinstrechner, z.B. ein Raspberry Pi, mit dem Bussystem der Maschine verbunden. Die Kommunikation der realen Maschine wird aufgezeichnet und an einen Cloud-Service übermittelt. Dabei können konkrete Ereignisse ausgewählt werden, bei deren Eintreten der vorangegangene Zeitraum nochmals mit einem entsprechenden Vermerk gesendet wird. Auf diese Weise lassen sich einzelne Fehlerszenarien schneller finden und analysieren. In der Cloud kann man die Daten mit flexibel angemieteter, bei Bedarf enormer Rechenleistung analysieren. Zusätzlich ist die Einbindung von unternehmensexternen Kompetenzen möglich.
Integration und Datenakquise
Für die Integration des Kleinstrechners gibt es mehrere Möglichkeiten. So können die Mitarbeiter im Außendienst bereits im Feld befindliche Systeme anbinden. Auch ein fester Einbau des Kleinstrechners in das Kundensystem ist denkbar. Für eine möglichst breite Abdeckung sollten vor allem neu verkaufte Systeme entsprechend ausgerüstet werden, entweder als Sonderausstattung oder als Bestandteil des Standards.. Darüber lassen sich große Mengen an Betriebsdaten generieren und analysieren, gleichzeitig wird für den Anwender die Anlagenverfügbarkeit erhöht.
Erwecken des digitalen Zwillings
Mit den nun vorhandenen Daten und dem Simulationssystem kann der digitale Zwilling erweckt werden. Dafür muss lediglich das richtige Programm auf die SPS aufgespielt werden und der virtuelle Bus dementsprechend konfiguriert werden. Daraufhin geben die Slave Stacks die Kommunikation der realen Maschine anhand der Aufzeichnung wieder. Das führt im Umkehrschluss dazu, dass sich die SPS samt verbundener Benutzeroberfläche gemäß ihrem realen Vorbild im Feld verhält. Dabei besteht die Wahl den Zwilling als Live-Version zu erstellen, gespeist aus einer laufenden Übertragung, oder als Rückblick, mit aus dem Archiv der aufgezeichneten Kommunikationshistorie stammenden Daten. Mithilfe des digitalen Zwillings können die Maschinenzustände und das Verhalten von SPS und Benutzeroberfläche analysiert werden. Zusätzlich kann das Simulationssystem im Anschluss auf dem Zwilling aufbauen, entweder durch manuelle Eingaben oder das Abspielen von selbst erstellten bzw. aufgezeichneten Szenarien. Damit kann das Verhalten des dargestellten Systems unter verschiedenen Einflüssen getestet und wenn nötig angepasst werden.
Anwendung in der Praxis
Die Firma Intravis ist Hersteller von Systemen zur optischen Prüfung von Kunststoffteilen. Typische Prüfobjekte sind Verschlusskappen und Vorformlinge für Flaschen sowie Aufdrucke und Etiketten von Verpackungen. Die beschriebene Entwicklung des digitalen Zwillings fand als Masterarbeit, in Kooperation mit dem Werkzeugmaschinenlabor (WZL) der RWTH Aachen statt, um eine Verbesserung der Serviceabläufe und Entwicklungsbedingungen zu erzielen. Die betrachteten Maschinen setzen sich aus drei Hauptkomponenten zusammen: einem Industrie-PC mit der Benutzeroberfläche, der SPS und dem angebundenen Bussystem und dessen Komponenten.
Intravis GmbH
Dieser Artikel erschien in INDUSTRIAL COMMUNICATION JOURNAL 1 2019 - 06.03.19.Für weitere Artikel besuchen Sie www.sps-magazin.de