Automatisierte Produktionslinie
Ein Rahmen in Roboterhand
Seit 1979 bahnt sich die Mercedes G-Klasse ihren Weg durchs Gelände. Dafür setzt man bei Daimler auf besonders stabile Leiterrahmen. Diese werden bei Magna Presstec im österreichischen Lebring gefertigt. Die dortige Produktion läuft seit 2017 vollautomatisch auf einer Linie von Kuka.
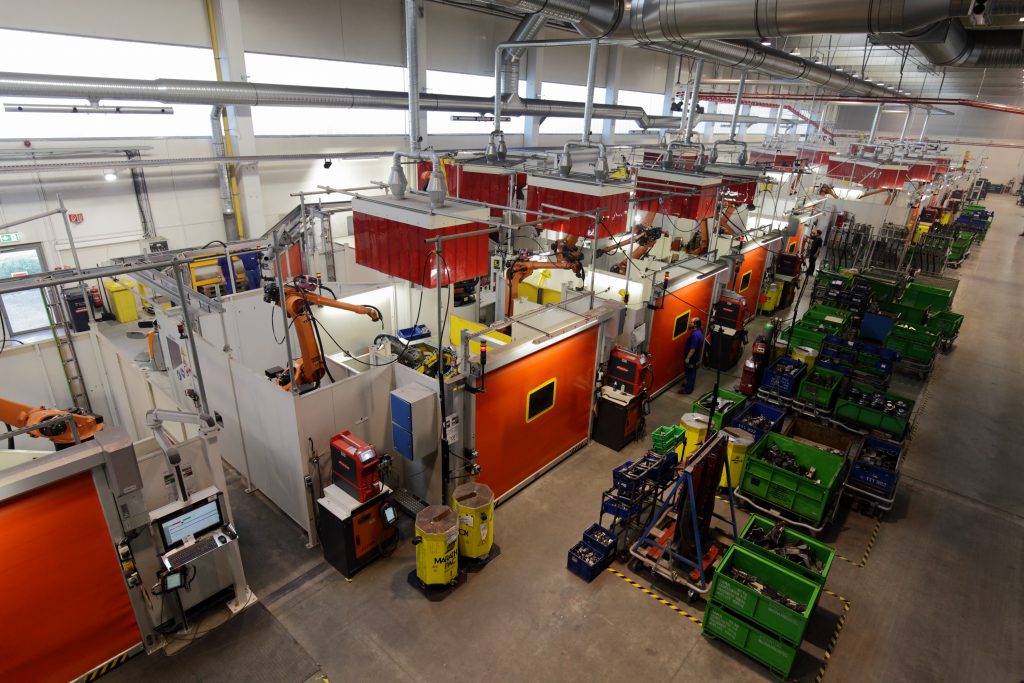
Das äußere Erscheinungsbild der Mercedes G-Klasse hat sich seit der Markteinführung nur wenig verändert. Und auch bei der neuesten Version lag der Schwerpunkt mehr auf der Technik als auf der Optik. Gleichzeitig hat sich in der Fertigung des Leiterrahmens, der bei Magna Presstec gefertigt wird, jedoch einiges Verändert: Wo vorher noch vieles von Hand geschweißt wurde, übernimmt nun eine automatische Produktionslinie des Roboterherstellers Kuka diese Arbeiten.
Individuelle Lösung für begrenzten Platz
Den Ausschlag für die Kontaktaufnahme mit Kuka gab eine Referenz mit ähnlicher Aufgabenstellung, die der Roboterbauer bereits vor einigen Jahren umgesetzt hatte. Den Startpunkt für das gemeinsame Projekt bildete ein Workshop. "Es war sehr positiv, die Ziele und Ansprüche beider Seiten zusammen zu visualisieren und damit in die Umsetzung zu gehen", erklärt Armin Kleemaier, Projektleiter bei Magna Presstec. Das anfängliche Grobkonzept der Anlage wurde im Laufe des Projekts immer mehr konkretisiert. Eine besondere Herausforderung war dabei die Hallengeometrie. "Die gesamte Produktions- und Logistikfläche beträgt etwa 2.000m². Jedoch ist nicht das gesamte Areal für die Produktionsanlage nutzbar. Hinzu kommt, dass die Produktionshalle sehr lang und schmal ist", sagt Dominik Pfeiffer, Projektmanager bei Kuka. Um den Platzverhältnissen Rechnung zu tragen, mussten individuelle Lösungen gefunden werden. Beispielsweise, indem auf der linken Hallenseite ein Versorgungsgang für Drahtfässer oder Roboterequipment angelegt wurde. Bauteil-Racks dienen zur Ablage der einzelnen Teile während des Produktionsprozesses. Hinzu kamen die Maße und das Gewicht des Bauteils: Bei einer Länge von 4,30m und einer Breite von 1,20m bringt der Leiterrahmen mehr als 230kg auf die Waage. Verarbeitet werden circa 145 Einzelteile. Die Gesamtlänge der Schweißnähte beträgt annähernd 80m, zusätzlich werden über 200 Schweißpunkte gesetzt.
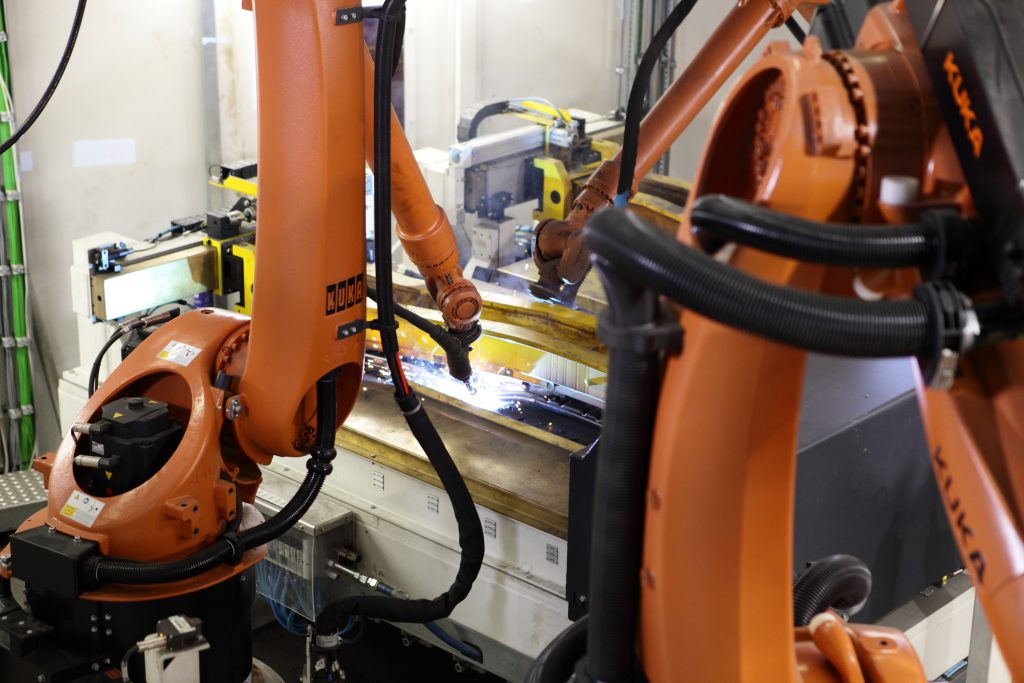
Gleicher Aufbau - nur spiegelverkehrt
Der Leiterrahmen setzt sich aus zwei Hauptgruppen sowie weiteren Einzelteilen zusammen. Die Fertigungslinien für den Vorder- und den Hinterbau sind von der Systematik her gleich aufgebaut, sind jedoch spiegelverkehrt angeordnet. Wesentliche Bestandteile sind dabei die beiden Squeezing-Stationen. Danach werden die teile möglichst verzugs- und spannungsarm verschweißt. Die nachfolgende geometriegebende Station (Geo-Station) verbindet die Längsträger mit den Querträgern und den Federdomen; ab diesem Zeitpunkt spricht man vom Vorder- bzw. Hinterbau. Die Besonderheit dabei ist, dass Heften und Ausschweißen nicht in separaten Schweißstationen, sondern direkt in den jeweiligen Stationen der Linie erfolgt. Nach dem Anbringen weiterer Kleinteile wird jede Unterbaugruppe am Ende der Linie einer Qualitätskontrolle durch einen Werker unterzogen. Erst danach legt ein Roboter das Bauteil in einem Rack ab, und es wird dem nächsten Arbeitsschritt zugeführt. In einer weiteren Geo-Station werden Vorder- und Hinterbau gemeinsam mit weiteren Einzelteilen zum Unterbau bzw. Leiterrahmen verbunden. In jeweils darauffolgenden Stationen werden die angebrachten Teile ausgeschweißt. Vor der Stanze ist noch ein Puffer vorgeschaltet, in dem die Bauteile auf eine einheitliche Temperatur abkühlen. Nach der Endkontrolle durch ein Inline-Messsystem und Qualitätsprüfer wird der fertige Leiterrahmen automatisiert zur Oberflächenveredlung übergeben.
Softwarelösung inklusive
Durch den Kuka-eigenen Standard MiKuka werden Informationen zum Maschinenstatus transparent dargestellt und standardisierte Funktionen erleichtern die Bedienung. Durch die Softwarelösung können Anwender Bedien- und Anzeigefunktionen erstellen und erweitern. "Durch diese Steuerung sind unsere Kunden in der Lage, im Sinne der Industrie 4.0 zu produzieren. Wir sorgen mit unserer Steuerungstechnik für die nötige Vernetzung, Selbstkonfiguration und Selbstdiagnose", sagt Dominik Pfeiffer.
45 Roboter im Einsatz
Seit Mai 2017 ist die Anlage verkettet und in Betrieb. "Das Schweißen läuft nun äußerst prozessstabil ab und wir erreichen mit geringem Personaleinsatz eine optimale Qualität sowie eine hohe Ausbringung", fasst Pfeiffer zusammen. Im Einsatz sind 45 Roboter, insbesondere vom Typ KR 30 L16 als Schweißroboter und KR240 als Handler. An einer abschließenden Inline-Messstation vermisst ein Roboter mit Kamera und Linien-Laser die Bauteile und sorgt dafür, dass die Rahmen zu 100 Prozent auf ihre maßlichen Merkmale wie Löcher, Bolzen, Kanten und Flächen geprüft werden. Dadurch soll eine konstante Bauteilqualität gesichert werden. In zwei Schichten erreicht Magna Presstec eine Ausbringung von 20.000 Leiterrahmen pro Jahr. Armin Kleemaier ist zufrieden mit dem Verlauf und dem Ergebnis. "Die Zusammenarbeit mit Kuka war gut und verbesserte sich im Lauf der Zeit noch weiter. Wenn Störeinflussgrößen aufgetreten sind, konnten wir auch diese immer gut abarbeiten. So haben wir das Projekt gemeinsam zum Erfolg geführt."
Seit 1979 bahnt sich die Mercedes G-Klasse ihren Weg durchs Gelände. Dafür setzt man bei Daimler auf besonders stabile Leiterrahmen. Diese werden bei Magna Presstec im österreichischen Lebring gefertigt. Die dortige Produktion läuft seit 2017 vollautomatisch auf einer Linie von Kuka.
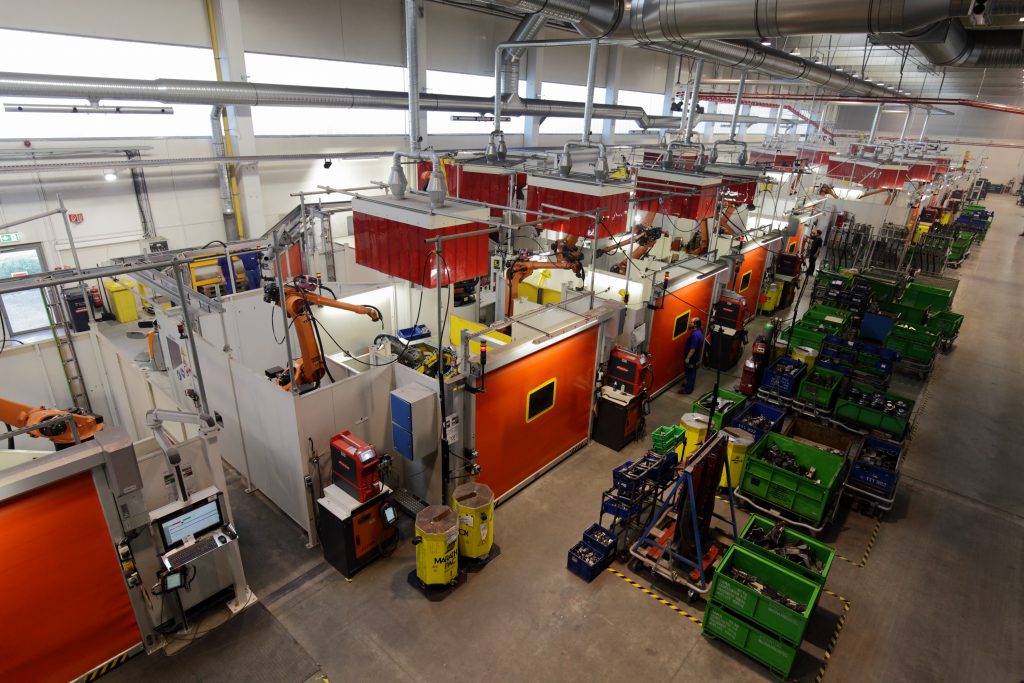
Das äußere Erscheinungsbild der Mercedes G-Klasse hat sich seit der Markteinführung nur wenig verändert. Und auch bei der neuesten Version lag der Schwerpunkt mehr auf der Technik als auf der Optik. Gleichzeitig hat sich in der Fertigung des Leiterrahmens, der bei Magna Presstec gefertigt wird, jedoch einiges Verändert: Wo vorher noch vieles von Hand geschweißt wurde, übernimmt nun eine automatische Produktionslinie des Roboterherstellers Kuka diese Arbeiten.
Individuelle Lösung für begrenzten Platz
Den Ausschlag für die Kontaktaufnahme mit Kuka gab eine Referenz mit ähnlicher Aufgabenstellung, die der Roboterbauer bereits vor einigen Jahren umgesetzt hatte. Den Startpunkt für das gemeinsame Projekt bildete ein Workshop. "Es war sehr positiv, die Ziele und Ansprüche beider Seiten zusammen zu visualisieren und damit in die Umsetzung zu gehen", erklärt Armin Kleemaier, Projektleiter bei Magna Presstec. Das anfängliche Grobkonzept der Anlage wurde im Laufe des Projekts immer mehr konkretisiert. Eine besondere Herausforderung war dabei die Hallengeometrie. "Die gesamte Produktions- und Logistikfläche beträgt etwa 2.000m². Jedoch ist nicht das gesamte Areal für die Produktionsanlage nutzbar. Hinzu kommt, dass die Produktionshalle sehr lang und schmal ist", sagt Dominik Pfeiffer, Projektmanager bei Kuka. Um den Platzverhältnissen Rechnung zu tragen, mussten individuelle Lösungen gefunden werden. Beispielsweise, indem auf der linken Hallenseite ein Versorgungsgang für Drahtfässer oder Roboterequipment angelegt wurde. Bauteil-Racks dienen zur Ablage der einzelnen Teile während des Produktionsprozesses. Hinzu kamen die Maße und das Gewicht des Bauteils: Bei einer Länge von 4,30m und einer Breite von 1,20m bringt der Leiterrahmen mehr als 230kg auf die Waage. Verarbeitet werden circa 145 Einzelteile. Die Gesamtlänge der Schweißnähte beträgt annähernd 80m, zusätzlich werden über 200 Schweißpunkte gesetzt.
KUKA AG
Dieser Artikel erschien in IT&Production September 2019 - 06.09.19.Für weitere Artikel besuchen Sie www.it-production.com